2024/2/19 9:43:50 点击:1318
摘要:目前国内硬质PVC制品普遍使用CPE做抗冲改性剂,《氯化聚乙烯》行业标准规定了九项质量指标要求,本文探讨了CPE这九项质量指标对硬质PVC改性的影响,找出对硬质PVC改性效果的影响趋势,确定一定的指标范围,对于PVC塑料加工具有一定的实际指导意义。
聚氯乙烯(PVC)因具有强度高、难燃、抗化学腐蚀等优点而被广泛应用于化工、建材等领域,是当今世界第二大通用塑料。然而,PVC的韧性较低,使其应用受到一定的限制,所以必须对其进行增韧改性。PVC异型材常用的抗冲改性剂有氯化聚乙烯(CPE)和丙烯酸酯类(ACR)冲击改性剂两大类。由于CPE性价比高,目前国内PVC-U制品使用CPE做抗冲改性剂的占80%以上。
CPE增韧改性PVC的效果主要与CPE原料、氯含量和制备条件有关,CPE用量为6~15份时,增韧效果最佳。CPE原料HDPE的分子量高,一般塑化慢,增韧效果好;分子量低,一般塑化快,适应高速挤出。用于PVC-U制品增韧改性时,氯含量在36%左右时CPE综合性能方面优越。实践表明,CPE的主要性能指标均对PVC异型材的改性效果有影响,尤其是CPE分子链上氯原子的分布以及熔融焓指标对CPE本身及其PVC共混物的物理性能、加工性能均有较大影响。因此HG/T 2704-2010《氯化聚乙烯》行业标准规定了九项氯化聚乙烯质量指标要求,下面分别就其对PVC改性的影响进行探讨。
一、不同熔融焓的CPE对PVC改性的影响
同一原料生产的相同氯含量CPE产品的性能差异主要是由熔融焓(残余结晶度)和氯原子的分布不同所导致的。氯原子在大分子链上的分布情况与氯化的工艺方法、氯化条件(温度、压力、氯化反应速度等)有关,而氯原子的分布状态决定CPE的熔融焓。氯分布受原料、氯化工艺条件影响较大,CPE氯化法生产制备中,氯化反应温度在原料聚乙烯的熔点范围内尽可能高的氯化反应温度和适合的通氯量,可以使氯化反应均匀,氯的分布更分散,原料HDPE的结晶消失,从而得到橡胶态良好的CPE。如果选择相对较低的反应温度进行氯化反应,可以使氯在PE分子上的分布不均匀,保持部分结晶态,虽然降低橡胶性,但能保持PE良好的电性能的特殊用途的CPE[1]。
因此,氯化聚乙烯可根据氯化工艺的不同,通过改变工艺条件控制氯的分布,尽管氯含量相同,但会得到非结晶性的橡胶弹性体和适度结晶的不同性能的产品。通常其结晶度大于15%的为结晶型,此类CPE具有较好的强度和韧性,常作为热塑性树脂使用,(也可以作为塑料改性剂)。当CPE结晶度小于5%时,此类产品为非结晶型,具有较好的弹性和低温性能,一般作为抗冲击改性剂和特种合成橡胶。
要想制得弹性好的CPE产品,必须在氯化时将HDPE的绝大部分结晶破坏形成无定型结构,但很难将HDPE的结晶全部破坏,不能破坏的结晶称为残余结晶,衡量指标就是残余结晶度或熔融焓,检测方法有溶解法和DSC法。通常残余结晶度3~6%以下(DSC检测结晶熔融焓2~4J/g以下)的CPE抗冲改性产品综合性能最佳[1]。在新修订的化工行业标准中,以DSC法测定CPE残余结晶度,以CPE熔融焓表示。熔融焓(DSC法)是目前常采用的方法,也是现在CPE标准中的一个重要检测项目,是影响CPE改性性能的一个重要指标。
实验发现,在CPE熔融焓0.6~4.7J/g的范围内,随着熔融焓数值的增加,塑化时间呈减少趋势,塑化呈增快趋势,但是差别不是很大。最小扭矩也随着熔融焓数值的增加而呈增加趋势。样品的最大扭矩、平衡扭矩基本一样,这可能是与HDPE原料相同、分子量相同因素有关。
通过添加不同熔融焓的CPE样品的PVC/CPE复合材料的缺口冲击强度、拉伸冲击强度和焊接强度的检测,也可以发现,随着CPE熔融焓数值的增加,不同熔融焓CPE所得的复合材料性能呈下降趋势,而当CPE熔融焓超过2.3J/g时,所制得的复合材料的拉伸冲击强度就会略低于600 KJ/m2。这可能是因为CPE熔融焓数值大,其PE链段较多,与PVC相容性较差的原因;而熔融焓对焊接强度影响相对小一点,可能是因为塑化快,塑化度高对焊接强度有利。
不同熔融焓的CPE对PVC/CPE体系的塑化时间、复合材料性能均有影响;氯含量为36%左右、熔融焓(DSC)≤1.4 J/g的CPE,比较适合作为PVC的抗冲击改性剂。熔融焓(DSC)作为衡量CPE性能的指标对于PVC塑料加工是具有实际指导意义的[2]。
二不同熔融焓的CPE对PVC改性的影响
CPE生产企业普遍采用水相(酸相)悬浮法氯化工艺,在氯化反应过程中,聚乙烯分子中的部分氢原子被氯原子取代,生成氯化聚乙烯和氯化氢。由于CPE的生产在悬浮液中进行,而且在此过程中有氯化氢产生,因此CPE产品中的挥发物既包含水分,还包含高温时从CPE分子内部挥发出的氯化氢气体。氯化氢对CPE,尤其是PVC的分解具有催化作用,会导致分解脱氯化氢反应速度大大加快,使PVC大分子的降解及断链分子间交联加剧,从而影响PVC制品的加工性能和机械性能[3]。实践表明,CPE产品的挥发物的质量分数(简称挥发分)指标对CPE本身及其PVC共混物的物理性能、加工性能均有较大影响,因此CPE的挥发分是氯化聚乙烯非常重要的技术质量指标。
CPE的生产工艺流程主要包括氯化反应、平板过滤、离心脱水、干燥、磨碎、涂覆包装等流程。离心脱水和干燥工艺过程的条件不同,会导致所生产的CPE的挥发分也会有差别。
根据CPE脱氯化氢实验结果发现,CPE的挥发分越高,其脱出一定浓度的氯化氢所需要时间越短,稳定性越差。这是因为CPE的挥发分越高,含有的水分、氯化氢气体等挥发物就多,氯化氢对CPE的分解同样起到催化作用,加快了CPE分解脱氯化氢速度。
通过流变实验发现,CPE挥发分越高,PVC/CPE复合材料的塑化时间越短,塑化越快。随着CPE挥发分的增大,塑化时间呈减少趋势,塑化呈增快趋势;最大扭矩和最小扭矩也呈增加趋势。所选CPE样品改性的复合材料平衡扭矩基本一样,这可能是与HDPE原料相同、分子量相同等因素有关。(如图1)
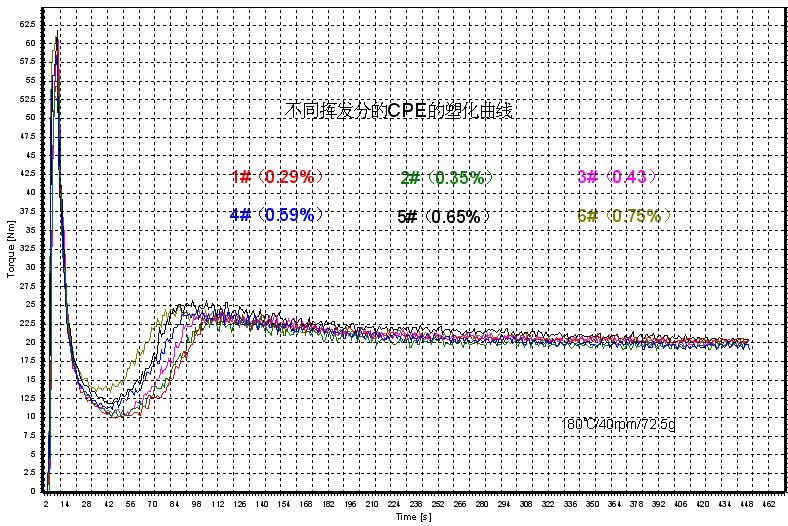
通过对添加不同挥发分的CPE样品的PVC/CPE复合材料的缺口冲击强度、焊接强度和型材表面色差的检测,可以发现,随着CPE挥发分的增大,不同挥发分CPE所制得的PVC/CPE复合材料的物理机械性能呈下降趋势,使用挥发分为 0.43%的CPE样品改性的复合材料的常温单V缺口冲击强度已经降低到只有20.2 KJ/m2;随着CPE挥发分的增大,复合材料型材色差(b值)逐步增大,型材表面出现发黄现象,而CPE的挥发分达到0.75%时,型材色差更大,型材表面发黄严重,其内筋和内壁已经出现发泡现象,这可能是因为CPE挥发分大,导致脱出氯化氢多,稳定性差,且塑化过快的原因。而焊接强度到挥发分 0.59%的CPE样品改性的复合材料仍较高,可能是因为虽然塑化快,但是塑化度高对焊接强度有利,直到挥发分0.65%的CPE样品改性的复合材料的焊接强度就明显下降了。
不同挥发分的CPE对PVC/CPE复合材料的塑化时间和物理机械性能均有影响;随着挥发分数值的增加,复合材料的塑化时间呈减少趋势,塑化呈增快趋势,且密炼块逐渐变黄;复合材料的物理机械性能随着挥发分的增加呈下降趋势。CPE的挥发分越高,其脱出一定浓度的氯化氢所需要时间越短,稳定性越差,这一规律与PVC/CPE复合材料的塑化快慢是一致的。氯含量为36%左右、挥发分≤0.43%的CPE,比较适合作为PVC的抗冲击改性剂。挥发分作为衡量CPE性能的指标对于PVC塑料加工是具有实际指导意义的[4]。
三不同门尼粘度的CPE对PVC改性的影响
尽管CPE行业标准中,门尼粘度对塑改型料没有要求,但是CPE的门尼粘度可以反映CPE的分子质量,CPE的分子质量对其物理性质有着重大影响,如材料的流动性、耐老化性、强度等。分子质量高则制品强度高,但是分子质量过大,黏度太大,会使经CPE改性的PVC 需要较高的加工温度才能成型,加工温度过高,不但给加工过程带来困难,也给产品本身的质量带来不良影响。因此,要保证制品的物理性能,并不要求PE 分子质量过高。CPE的专用原料HDPE分子质量通常控制在10万~15万。以PE 的熔体流动速率来表征PE分子质量,熔体流动速率与分子质量成反比。CPE门尼粘度的高低也能反映CPE分子质量的大小,门尼粘度高的CPE分子质量大,门尼粘度低的CPE分子质量小。
根据流变曲线实验结果发现,CPE门尼粘度的不同,导致CPE的流变性能不同,塑化时间随着CPE门尼粘度的升高而延长,在流变性能上的差异反映为塑化时间的延长,在加工应用实验中则反映为挤出机扭矩的降低,并且挤出机扭矩降低的幅度与塑化时间延长的幅度有一定的规律可循。
用转矩流变仪所检测的物料流变性能能够比较真实地反映CPE的加工性能,塑化时间的快慢与挤出机扭矩的高低相对应,即一般情况下塑化快,扭矩高,此时物料摩擦热增多;塑化慢,扭矩低,产生的摩擦热较少。虽然实验配方与加工工艺条件不同,但不会影响这种趋势[5]。
从挤出机所生产的型材性能指标分析发现,分子质量大的CPE所制得的PVC/CPE复合材料型材性能相对较高,抗冲击改性效果较好;低分子质量CPE,其PVC/CPE复合材料的冲击强度有下降趋势[6]。
因此实际应用中,并非塑化越快的CPE使用情况越好,应结合加工厂家的实际生产配方及加工工艺来具体选择。
四不同氯含量的CPE对PVC改性的影响
CPE与PVC共混时的相容性,取决于CPE的氯含量多少和氯原子在PE分子链上的分布情况。CPE中含氯量大小对PVC改性效果影响很大,同一种聚乙